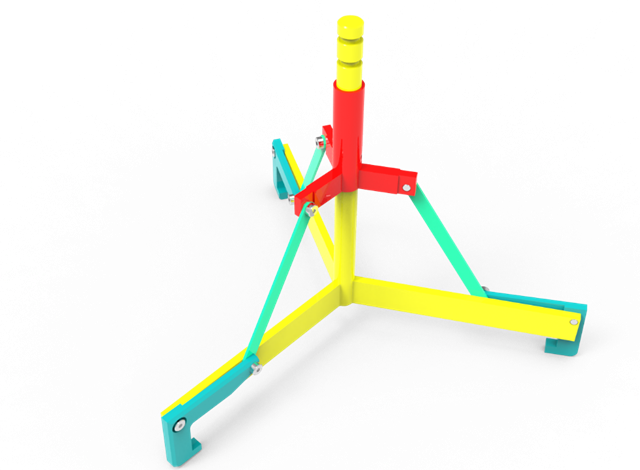
This project involved the design and development of a robotic claw mechanism tailored to very specific client requirements. General requirements included the mechanism using least number of moving parts possible, easy to manufacture, maintain and repair.
Robotic Claw Model
Tasks
The client sought a proof-of-concept model that should be
- capable of lifting 515 mm diameter disc shaped object with thickness ranging from 22 to 25 mm.
- able to approach from top and securely grip the object while it is placed on a platform of about 50 mm height.
- able to work with single servo motor for gripping mechanism.
- The project highlighted use of minimal design without sacrificing any functionality of the product.
Actions:
Given the requirements, it was obvious that I needed some sort of claw mechanism. To determine how much simple or complex the mechanism and what it’s capable of, I drew some general design constraints. These were
- The mechanism can be specific to only disc (as is obvious) shaped objects.
- Whatever is used to grip the disk, should not be in place until the disk is touching the very top surface otherwise the disc would not be able to get within the claws.
- Since it is disc shaped, I need at least 2 claws to hold secure it properly. But 2 claws might not be enough given if the weight of object is too much.
- To avoid the flipping of disc, I would need to increase the width of claw which might interfere with ground or platform. In that case, I would either have to increase the clearance, or introduce a third claw.
- Once placed, since the claw will be moving upwards, the model will be so that the grip tightens under gravity as to help keep model in place.
Design Process:
Based on the constraints mentioned, I came up with a simple mechanism that converted linear up and down motion of a collar on metal post into circular motion of claws. Under this design,
- I came up with a simple 2 bar mechanism that was well suited to lifting disc like objects.
- Using a circular motion of claws, I was able to stay clear of disc edges while approaching it from top.
- After some initial designs, I quickly understood that my intuition about clearance issues with 2 claw model was right. I knew I will be needing 3 claws at least to accomplish this task.
- Once the collar was lifted up, the entire post would be lifted up to create a strong grip under gravity.
For software, I decided to go with SolidWorks. The main reasoning to choose SolidWorks was its easy to manage assembly features that link very easily to main part files. Moreover, SolidWorks has some great drawing tools should I need that in future.
I had clear idea of what the object dimensions were and how it will be placed, so based on that, I drew circles around the joints around the joints to determine their positions in advance before creating model. This simple yet effective approach saved me a lot of time on manual calculations and hand drawings. It also showcases my use of simple techniques to come up with solutions on the fly during the design process rather than drawing something on paper first.

Results
Finally, I created the claw model so that the central post had 3 claws at an angle of 120 degrees from each other. The claw model had ample clearances and met the conditions to lift the disc objects. The inner section of each claw corresponded to diameter of about 520 mm. The extra 5 mm in diameter was for clearance purposes. The linear motion was supposed to be driven by attached screw jack mechanism loaded on top of the post but unfortunately the client only needed proof of concept and this was enough.


Leave a Reply